
金型製作における「キャメスト」の活用(1/2)
〜3次元データ活用を見据えた2次元CAD/CAM「キャメスト」〜
(「型技術 2008年5月号」掲載)
|
弊社は 、“3次元形状処理技術”と“データ変換技術”をベースに、3次元データ流通や活用のためのソリューションを長年にわたり提供してきた。この度、これまで培ってきた技術を新規分野へ展開するべく、2次元CAD/CAM『キャメスト』を発売した。
今回、本誌5・6月号のSpecial Reportを通じてキャメストを紹介するにあたり、まず5月号でキャメストの開発背景や製品機能など全体像について述べ、6月号では金型製作におけるキャメストの導入事例を紹介していきたい。
■開発背景
(1) 3次元データ流通の現状
設計/製造工程の隅々にまで3次元データを行き渡らせ、それを他部門やサプライヤで有効活用することでプロセス全体の生産性を高め、製品の競争力を向上させることができる。実際に、自動車メーカーや大手電機メーカーの設計工程では3次元データが多くの分野で活用されている。特に自動車業界では、JAMA(日本自動車工業会)やJAPIA(日本自動車部品工業会)が3次元データの品質基準を作成するなど、3次元データ活用が進んでいる。その一方で、多くのサプライヤの製造工程では、未だに2次元図面を中心としたモノづくりが行われており、3次元データが有効活用されているとは言い難い(図1)。
図1. 3次元データ流通の現状
3次元データ活用が進んでいる自動車業界でさえ、実加工・仕上げ・組み付け・トライ補正などの製造工程では、3次元データがあまり活用されていない。
その原因としては、
@3次元ツールが高価で、操作も複雑である(もしくはそのように思われている)
A現状の2次元ツールが3次元データを十分に活用できない
B加工の大半は2次元加工であるため、加工現場では2次元データを好む傾向がある
ということなどが挙げられる。
しかし、3次元データに盛り込まれた形状・フィーチャー・属性などの情報を製造工程に上手く渡すことが出来れば、製造工程においても高い効果をあげることができる。また、製造工程で3次元データが普及すれば、製造工程の情報を設計工程にフィードバックすることができ、サプライヤとのコラボレーションの観点でも非常にメリットが大きい。
3次元データ流通・活用はまだまだ一部の工程に閉じており、3次元データに盛り込まれた情報は、宝の持ち腐れになってしまっている。この現状を打破するため、弊社は、3次元データに盛り込まれた情報を有効活用する「簡単・低価格・高性能」な2次元CAD/CAM“キャメスト”の開発に着手した。今回その第1弾として、3次元データ活用のベースとなる2D CAD・マシニング 2D CAM・穴加工 CAM・ワイヤー放電CAM・NC チェッカーを2008年4月7日にリリースした。
キャメストが加工現場への3次元データの導入口となることで、設計/製造のあらゆるプロセスで3次元データを合理的かつ効率的に使い尽くす、真のデータ一気通貫の実現に寄与できると確信している。
(2) 加工現場におけるCAMの現状
読者の多くの皆様は、キャメストの開発に対して「何故今さら2次元CAM?」と怪訝に思われたかもしれない。確かに2次元CAM開発は、3次元CAMの多軸・複合加工対応が盛んな近年のCAM開発の流れとは逆行している。しかし、技術のトレンドではなく現場のニーズという観点から見ると、多くの場合3次元CAMはオーバースペックであり、2次元CAMの方がマッチしていることが多い。事実、未だ多くの現場では2次元CAMが活躍している。理由は、以下の2点にある。
i) 現場の加工の大半は2次元加工である
部品形状に自由曲面は少なく、むしろ穴・ポケット・溝といったシンプルな形状が多い。自由曲面を比較的多く含む金型加工も、射出成形用金型やプレス用金型の抜き型はほとんどのものが2次元加工で製作することができ、その例外ではない。もちろん、意匠面など製品機能に自由曲面が必要とされる部品の場合は、3次元加工を多く必要とするが、そのような部品は全体から見れば非常に少ない。
ii) 2次元加工には2次元CAMの方が適している
3次元CAMが2次元CAMの性能を包含するような誤解があるが、一般的には3次元CAMは2次元加工が苦手である。シンプルな2次元加工では、2次元CAMの特長である“手軽さ”を十分に活かした方が良い。以下に、その例を示す。
(a) 輪郭加工
2次元輪郭加工において2次元CAMは、工具径補正の指令をするNCデータを作成することができる。そのため、寸法の微調整を行いたい場合には補正量を調整するだけで良く、再度作図してNCデータを作成する手間がない。また、あらかじめカッターパスを製品位置で出しておき、工具径に応じて工作機械側で補正しながら加工することにより、粗加工から仕上げまでいくつものNCデータを持つ必要がなくなる。工具径補正の指令をするNCデータを作成できることにより、融通の効く加工が可能になる。
(b) 穴加工
3次元CAMにおいてモデリングされた形状から穴を抽出する場合、一般的にはモデルから穴を探して認識させる必要があり、非常に手間がかかる(ただし、フィーチャー認識のように簡単に抽出できることもある)。一方2次元CAMでは、CAD図上の円形状から穴を選択するだけで良いため簡単である。また、穴の範囲指定選択ができるので、多数の穴がある形状でも短時間でNCデータを作成することができる。
(c) ポケット加工
3次元CAMの多くは曲面を一度ポリゴンに変換してからカッターパスを計算する方式を採用しており、円弧補間のカッターパスは直線分割されてしまう。そのため、精度が悪くNCデータ量も多くなってしまう。2次元CAMでは、G02、G03の円弧補間指令としてNCデータを出力できるため、精度が高くNCデータ量も少ない。つまり、2次元CAMを用いた方が加工時間を短くできる。また、3次元CAMでモデリングを行うことと比べ、2次元CAMの場合は輪郭形状を作図するだけで良いため、簡単な作業で済む。
上記のように、現場の加工の大半は2次元加工であり、かつ、2次元加工には2次元CAM
が適していることから、未だ多くの現場では2次元CAMが活躍している。この現状を踏まえ、キャメストは2次元CAMをベースとしている。
■製品概要
冒頭で述べたが、サプライヤの製造工程で3次元データがあまり活用されない原因の1つに、3次元ツールが高価で、操作も複雑である(もしくはそのように思われている)ことが挙げられる。そのためキャメストは、多くの加工現場で受け入れられるように「簡単・低価格・高性能」という3つの特長を追求している。
i) 簡単
キャメストの“簡単さ”を表す1つの例が、絵や図を多用したユーザーインターフェースである(図2)。あくまで “現場の人にとっての分かりやすさ(現場感覚)”を重視しているため、ユーザーインターフェースは、敢えてWindowsに準拠していない。初心者や普段コンピュータに慣れ親しんでいない場合、Windowsに準拠したユーザーインターフェースが分かりやすいとは限らないからだ。
絵や図を用いているので直感的に機能を把握することができ、初心者でもすぐに簡単にNCデータを作成することが可能である。
図2. 分かりやすいユーザーインターフェース
ii) 低価格
ベースとなる2次元CAD/CAMとNCチェッカー(NCデータの確認・修正・通信ソフト)の組み合わせで266,700円と、導入しやすいリーズナブルな価格体系を実現している。3次元CAMはもちろんのこと、2次元CAMの中でも低価格帯に設定し、最上級の投資対効果を提供することを目指している(図3)。
図3. キャメスト価格表
製品名 |
価格 |
2D CAD |
\58,800 |
マシニング 2D CAM |
\149,100 |
穴加工 CAM |
\149,100 |
ワイヤー放電 CAM |
\149,100 |
NCチェッカー |
\58,800 |
iii) 高性能
キャメストは、加工現場向けのNCソフトウェアの開発で豊富な実績を持つ
株式会社キャドテック(*1)との共同開発である。
18年にわたるキャドテック社の技術の粋を結集し、机上の空論ではなく、現場の生の声を反映したCAMとなっている。現場のニーズを無視したオーバースペックな機能を開発するのではなく、工具の負荷を考慮した加工軌跡や送り速度など、現場のニーズにきめ細かに応えることを主眼としている。
(*1) 株式会社キャドテック(http://www.cadtec.net/)
浜松合同(株)(現 (株)ゴードーソリューション)や(株)放電精密加工研究所などのNCソフトウェアを開発するなど豊富な実績を持つ。
■機能紹介
以下にキャメストの機能をいくつか紹介する。
(1) 2D CAD
端点・交点の自動表示や補助線機能、高機能電卓など、面倒な座標計算を軽減するための様々な機能を備えている。インボリュート歯車もパラメータ指定で簡単に作図することができる。
(a) 微小端点自動接続 および 重複図形の削除
IGESやDXFなどの外部データをCADに取り込んだ際、図形が微小分割され端点が離れてしまうことや、線分が重複してしまうことがよくある。このような状態でNCデータを作成すると一般的にエラーになることが多い。また、微小分割された図形や重複した図形を探して修正するのは非常に手間がかかる。そのため、端点同士を自動で繋ぐ機能や重複した図形を削除する機能が備えられている。これらの機能があることにより、図形のトリムや延長をする作業が省けるなど図形修正にかかる時間を短くすることができる。
(b) オフセット
CADのオフセット機能により、工具径補正を使わない補正軌跡を簡単に作成することができる。アウトコーナーのオフセット時には、コーナー部をピン角かRにするかを選ぶことが可能である。ピン角の場合、工具の負荷が大きいコーナー部におけるF値をCAM側の設定で自動調整できるため、現在主流である高速加工にも対応している。
(c) スプラインパラメータの設定
工作機械にバックラッシがあるため、スプラインでなめらかな加工を行う場合には、円弧と円弧のつなぎ目の接線角度が重要になる。そのため、用途に合わせて自由曲線の作図方法を選択できるようになっている。
(2) 2D CAM(マシニング・穴加工・ワイヤー放電)
キャメストでは、輪郭加工、ポケット加工、島残し加工、追い込み加工、トロコイド加工、文字加工、多数個取り、穴加工、ダイ加工、パンチ加工、オープン加工、コアレス加工、上下異形加工などの様々な加工を行うことができる。
(a) Zアプローチパターン
一般的に領域加工においてはZアプローチ時に加工物に直接削り込んでいくと考えられるので、工具に対する負荷を減らすためにヘリカル下降が必要とされる。しかし、工作機械によってはヘリカル動作機能を使用できない場合がある。その場合は、ヘリカル下降の替わりにジグザグ下降を行えると便利である。そこで、2次元の領域加工におけるZアプローチパターンは、垂直下降の他にヘリカル下降とジグザグ下降の2種類を備えている。
(b) 工具リスト
加工物の材質によって加工条件が違うため、様々な材質を加工する場合、カッターパスを計算するたびに加工条件を入力する必要がある。そこで、材質別に加工条件を管理できる工具リストというデータベースを備えている(図4)。材質別に加工条件を工具リストとして登録しておくことで、加工条件を毎回入力する手間が省け、NCデータを作成するまでの時間を短縮することが可能となる。工具リストがあることにより、新人でもベテランと同じ加工条件を簡単に設定することができる。
図4. 工具リスト
(c) Z方向条件の設定
工具への負荷や仕上がり精度を左右するZ方向の切り込み量やF値を設定することができる(図5)。加工終了時のZ位置は仕上げ代までか終了のZまでかを選べるため、粗加工で仕上げ代分残したい時は、加工終了のZ高さを変更する手間を省くことも可能である。
図5. Z方向条件の設定
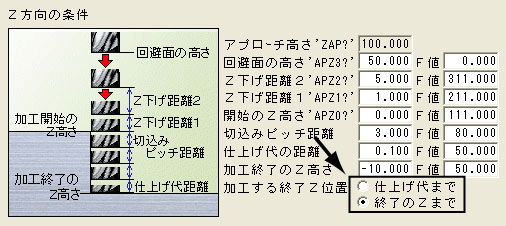
(d) 穴加工手順の設定
穴あけにおいて加工手順を事前に設定しておくことで、ドリル・タップ・リーマなどの加工パターンを円に指示するだけで工程を作成することができ、円に対して何回も加工手順を指示する手間を省くことが可能である(図6)。1度設定すれば新人でもベテランと同じ加工手順を簡単に設定することができ、非常に便利である。
図6. 穴加工手順の設定
(e) 穴あけにおける自動工程統合
ドリル・タップ・リーマなど複数の穴加工パターンがある場合、優先工具順を事前に設定しておくことで、センタードリルなどの前工程を自動でまとめる機能を備えている。これにより加工手順を修正することなく、工具交換の少ないNCデータを作成することができる(図7)。
図7. 工程統合例
(f) ワイヤーカットにおける豊富な加工パターンやアプローチ方法
ワイヤーカットでは、熱変形や切り落としのタイミングなどを考慮する必要があるため、多くの加工パターンを備えている(図8)。
図8. ワイヤ放電加工における豊富な加工パターン
また、精密に仕上げ加工を行っていく2ndカット以降は全面が放電する1stカットに比べて大きな放電エネルギーを発生しないため、アプローチ方法も1stカットと2ndカット以降で別々に指定ができるようになっている(図9)。
図9. ワイヤ放電加工における豊富なアプローチ方法
(g) 豊富なサンプルポストファイル
キャメストでは、ファナック、OSP、ソディック、ブラザー、マキノ、三菱、日立、シャルミー、セイブ、大隈豊和などの豊富なサンプルポストファイルを備えており、日本の工作機械のほとんどに対応することができる。
(3) NCチェッカー
NCチェッカーは、作成したNCデータの確認・修正・通信のためのソフトである。サブプロや工具径補正軌跡を描画することも可能である。ファナック、OSP、東芝、三菱といったサンプル設定が備えられているので、購入後すぐに描画することができる(図10)。
図10. NCチェッカー
■今後の展開
冒頭でも述べたが、自動車メーカーや大手電機メーカーでは3次元データが多くの分野で活用されるようになった。3次元データには形状・フィーチャー・属性などのモノづくりに有用な情報が盛り込まれており、それを解析や型設計、工程設計などに活用することで、開発期間短縮・コスト削減・品質向上といった効果を上げている。しかし、サプライヤの製造工程では、未だに2次元図面を中心としたモノづくりが行われており、3次元データが有効活用されているとは言い難い。設計/製造工程のどこかで3次元データに盛り込まれた情報が抜け落ちているのだ。
読者の中には、3次元データというと敬遠される方もいるかもしれない。しかし、3次元データに盛り込まれた情報は3次元ツールにしか使えないものではない。3次元データを2次元ツールで簡単に活用できるよう、上手く加工して渡すことで有効利用も可能だ。そうすれば、現場に浸透している2次元CAMでも3次元データを活用することができる。現状でも、3次元データを投影することで、2次元CAMでの作図の手間を省くというようなものがあるが、3次元データに盛り込まれた情報を十二分に活かしているとは言えない。3次元データがあれば、形状情報から生産要件を満たすかどうかを事前に判断することが可能になる。また、将来的には形状情報と属性情報から自動で工程を設計することも可能になる。
3次元データは加工現場にとっても宝の山である。普及している3次元データに盛り込まれた情報を無駄にせず、加工現場においても活用することが必要だ。2次元CAMは技術的に成熟期に入っているが、3次元データの活用という点ではまだまだ黎明期と言える。今後は、キャメスト上で3次元データを簡単に活用するための製品を発売していく予定である。
* * * * * * * * *
中国など新興諸国の台頭により、より一層の開発期間短縮・コスト削減・品質向上が求められている。日本の加工現場が勝ち残っていくためには、ITを効果的に用いることで、より付加価値の高いモノづくりを行っていく必要がある。言うなれば、“伝統的な職人”から“IT武装したマイスター”への転換である。弊社としても、パッケージソフトウェアを独自開発する数少ない日本企業として、今後とも日本の加工現場の進歩と発展に寄与できるよう尽力していきたい。